The key to efficient power conversion lies in the switching that occurs within the power stage of a dc/dc converter. For good reason, many of today's high-frequency high-performance PWM controllers do not have the capability to drive a power MOSFET directly.
Instead, a MOSFET driver IC is the interface between the low-power switching signals of a PWM and the high-current demanded by the MOSFET. Once a converter topology梥uch as buck, boost, forward, or full-bridge梚s decided on, selecting the best driver IC for a given application requires an understanding of the MOSFET driver IC functions most important to enhancing switching performance.
Input stage
The input stage of a MOSFET driver should be compatible with both CMOS and TTL input signals. CMOS input stages use variable input thresholds that depend on turn-on and turn-off thresholds equal to two-thirds of VDD and one-third of VDD.
CMOS input stages offer excellent noise immunity, especially for higher VDD values. Because a TTL input stage does not depend on matching the driver's VDD, the designer thus has more flexibility in choosing a PWM controller since UVLO is not a consideration for input-switching thresholds.
Output current rating
The driver's current rating and the power MOSFET gate charge predominately determine how quickly the MOSFET can switch on and off. Since these switching transitions determine the switching losses within the power MOSFET, choosing a driver with a current rating correctly matched to the power MOSFET can play an essential role in improving efficiency.
Earlier MOSFET drivers were designed using a complementary bipolar process to deliver the high current required by the power MOSFET. These types of drivers are effective at sourcing high current, but their ability to fully hold the power MOSFET in a high or low state is limited by their saturation and cutoff voltage.
Most modern MOSFET drivers use a MOS-only output stage to deliver the high current required by the power MOSFET of the dc/dc converter. ICs using MOS-only drive stages overcome the drawbacks of bipolar MOSFET drivers by fully switching the power MOSFET between the two power rails, VDD, and ground. The disadvantage of a MOS-only driver IC is its inability to source high gate current at low voltage, such as the power MOSFET gate-to-source threshold voltage.
Some manufacturers "address" this by specifying a "peak" current rating for such a device. For example, the test conditions for a MOS driver rated at 3 A might be specified at VDD of 10 V, equating to a driver source impedance of 3.3 W.
This means the driver can deliver 3 A of current when 10 V is applied across the gate and source of the power MOSFET. However, the power MOSFET doesn't begin to "turn on" until the gate-to-source threshold voltage is reached. Using an approximate value of 5 V for the power MOSFET gate-to-source threshold voltage means the driver's actual current rating is
(10 V – 5 V)/3.3 W = 1.5 A
which is only half the value specified on the datasheet.
As an example, MOSFET drivers such as the company's UCC37321/2 low-side 9-A driver consists of a combination bipolar and MOS process known as TrueDrive (see Fig. 1). The bipolar section provides the rated current where it is needed most, at the Miller plateau of the power MOSFET.
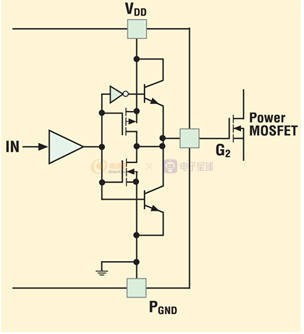
Fig. 1. The best MOSFET drivers for high-speed switching consist of a combination bipolar and MOS process.
The MOS section is placed in parallel with each bipolar device to achieve true rail-to-rail switching between VDD and ground. The result is a superior MOSFET driver optimized for high-speed switching and truly rated to deliver the full-current specified on the datasheet.
Internally regulated or adjustable gate drive
Some MOSFET drivers use a fixed internal regulator to set the amplitude of the gate drive voltage. Internally regulated gate drives should be considered when the VDD supply voltage to the driver IC is not well regulated.
The advantage is that the gate drive amplitude is well regulated and can be closely matched to a power MOSFET offering optimal switching results. However, as the gate-to-source voltage of a power MOSFET is increased, the on-resistance is decreased resulting in lower power dissipation from conduction losses.
Conversely, as the gate-to-source voltage is increased, the power losses associated with gate charge are also increased. Therefore, for converters requiring highest efficiency, such as voltage-regulator-module applications, a MOSFET driver with an adjustable gate drive voltage might balance the gate charge losses against conduction losses more efficiently.
Propagation delay
Propagation delay is the time it takes to pass a signal from the driver's input to output. While propagation delays can affect the timing between the PWM and the power MOSFET, the delay is not a primary concern because it is normally accounted for within the converter's control loop. For isolated converters using a primary-side PWM controller and a secondary-side synchronous rectifier MOSFET driver, propagation delay can significantly affect the timing of the primary to the secondary.
A requirement for these types of converters is that the total delay to the secondary synchronous rectifiers must be less than the delay from the PWM through the power transformer. Using a secondary-side MOSFET driver with a propagation delay larger than the primary-side PWM to MOSFET delay can make it difficult to optimize the timing between the primary and secondary.
Deadtime control
For synchronous buck dc/dc converter applications, the high-side and low-side MOSFETs must not be allowed to conduct simultaneously or destructive "shoot-through" currents can result. Therefore an important consideration for these types of MOSFET drivers is deadtime control.
Current drivers offer a user-programmable fixed delay between the two drive signals of a synchronous buck. The advantage of this approach lies in its simplicity. The disadvantage is that programming the deadtime long enough to ensure that cross conduction will not occur under all operating conditions results in additional body-diode conduction losses in the low-side synchronous MOSFET.
Others梥uch as the TPS2838/9 synchronous buck drivers梪se an adaptive gate drive technique to actively adjust the amount of deadtime between the high-side and low-side MOSFETs. Adaptive gate drive senses the drain-to-source voltage of the low-side MOSFET while actively adjusting the dead time to reduce body-diode conduction losses and avoid cross-conduction. Adaptive gate drive offers significant improvements over fixed-delay, but still suffers from the fact that some body-diode conduction is inevitable due to finite propagation delays between the time that body-diode conduction is detected and the gate drive signal is adjusted.
New drivers today also use a predictive gate drive to overcome the propagation delays associated with adaptive gate drive. Predictive gate drive technology is a digital-control technique that virtually eliminates body-diode conduction while optimizing dead-time to give the highest possible efficiency.
Packaging
As with any power management IC, the junction temperature of a MOSFET driver must be kept safely within rated limits under all operating conditions. Industry-standard packages such as DIP, SOIC, and TSSOP are popular considerations, but high-current MOSFET drivers used in high-frequency applications require careful consideration given to advanced packaging techniques.
Today's MOSFET drivers are placed in TSSOPs with an exposed leadframe die pad on the bottom of the package. This is known as a PowerPad TSSOP, or HTSSOP, offering thermal impedance with a junction-to-case rating as low as 2°C/W.
Compared with a TSSOP without PowerPad operating at similar junction temperatures, the lower thermal impedance of the HTSSOP means more power can be dissipated within a comparably sized package. For applications where minimizing parasitic effects such as stray capacitance and lead inductance are crucial for switching performance, the QFN package is a must. QFN packages have no measurable lead inductance, making them ideal for high-frequency converter designs.
Additional considerations
Secondary MOSFET driver IC considerations would include additional "features of convenience" not associated with driver performance enhancement. These might include such features as EN (Enable), overvoltage protection, thermal shutdown, or overcurrent protection.
Because MOSFET driver ICs are used in a variety of isolated and nonisolated power converter applications, a final note of consideration would be having access to a solid knowledge base of technical support. This support can often mean the difference between design success and failure.