求助14串锂电保护方案
如果用MCU怎么样?有没有那种16到20个AD通道且价格低廉的MCU,麻烦各位前辈推荐一下.
我主要想做一个电动车锂电池的保护板,可以保护36V或48V.
希望各位前辈多帮帮忙,我是一个新手.
你就根本不需要想的.
要是我老板叫我做,我根本就不需要理他.
告诉为什么做不了,做出来了也不顶个屁用.
那还不如10元也可以省了,不要保护板得了.
哈哈
双面PCB:1.5元;三星单片机S3F9454 2.2元;功率MOSFET2个:4.3元;电压和电流检测:7元;平衡电路不算在内的话,用单片机做,最便宜的方案至少也要15元以上的,估计你只能用保护IC的方案做。10元以下是根本不可能的事。如果不做平衡的话,你要是用国产电芯,电池组的寿命会极短的,这种板做出来,也是害人。:)
主控芯片采用ATmega48,其有8通道10bitAD。
由于要保护14S锂电池,每一个电芯都要采集电压,所以至少要有14个AD口。除去单片机只带的AD口,还需要6个AD口。
方法1:通过两个ATmega48进行采样,两个MCU有16个AD口,足够给每一电芯采样
方法2:通过普通口模拟AD口以达到电压采样。模拟方法采用电容在恒流下充电与时间成正比,结合单片机的定时器,利用程序进行电压的 间接采样。
另外由于14S锂电池,电压可能达到60V以上,所以通过电阻分压后,在通过AD进行电压采样。
电流则通过精密电阻进行采样,同样可以用AD采样得到电压后,得出电流值。
平衡电路则采用最简单的方式:恒定分流电阻均衡。
然后通过MCU进行充放电的控制。
14S的锂离子电池,充满时的电压接近60V了,因此如果直接电阻分压后进行电压测量,分辩率只有60V/1024=60mV,(1024为10bitA/D的分辩率),即使有软件校准,最小的误差也会有60mV,这种电压精度做保护都不够用,用来做平衡的话,平衡完压差也在60mV以上了。
因此如果你要用10BIT的A/D检测高位的电芯电压,必须要做电压变换,电压变换有几种方式,但是都需要钱,常用的有运放进行变换。
又:三星单片机S3F9454有9路的10BIT的A/D,只有2元2,比ATMEL的还便宜,如果你要想成本更低,可以用它。
如果你是新手,并且是公司小的话,我建议你放下单片机的方案,这个方案对于一个新手来说能在一年内玩下来都算你很有成就了,所以还别走这一条弯路,如果只是玩玩样品当然问题不大,但是要上量且可靠,这不儿戏,单片机保护,有很多优势和不足,对于新手根本无法兼备,对于锂电的精度你至少做到50MV的精度,并且是最大值50MV,如果是+/-50MV那么电池过充的时候,极端情况下,你就有可能出现0。1V的压差,这对锂电有很大影响,比如一个充到4。2V,而另一个就可能只有4。1V(我这只是简单说明,因为这里面还有很多其因素)。所以单片机很难做到50MV这个精度,我曾经用12位精度单片机也只能做到35MV,再往上做成本就大很多,无法跟市面产品做竞争,目前市面上有几种单片机大致有三种方案,电阻分压,电压差分,悬浮地电位采样,但却有多种做法,根据不同使用场合有不同使用优势
电压差分这种电路优点成本低,
缺点:1。精度差,并且有误差叠加,也就是当一个通道有50MV的误差时,14串整组电压就有0。05*14=至少就有700MV的叠加误差(如果按设计一一计算,至少也有1。5V的误差),因为电阻分压基本上是做减法。还有,由于你是多通道采样,这里还存在时间误差导致的检测误差,通道越多,这误差越大。
2。精耗电流大,并且分布不均匀,由于是用5V供电,采集14串,那么必须得做电阻分压,14*4。3/5=12。04倍,留一定余量,用电阻上限120K,下限10K进行分压采样,那么就会存在静耗电流,第一节静态电流为最大4。2/130K=32UA,最小19UA,最高节4.2*14/130K=450uA,最小269uA,从静耗上看,高节和低节静耗电流相差太大,不难算出,半年待机时间,就会有6%的容差。从精度上看,由于单片机采样需要一定的采样电流,不同品牌有所不同,一般大于5UA方能准确采样,那么可以根据电路大约等效单片机内部相当于一个下拉电阻5/5UA=5M,也就是说每个单节电池下拉电阻多并了一个5M电阻,这样对于不同节数导致的偏移也不一样。所以这采样的方法和时间,很重要,当然根据以上的缺点也可以做一些优化。比如电压跟随,等等!
对新手来说,用单片机做的确难度比较大,会有一些困难,不过从我目前所见过的所有方案来看,用单片机做的方案,检测精度最高,实际测试中,对每节电芯的电压最大测量误差,只有5mV.只是这种测量方法要用到一种电压变换电路,这种电路是我司已申请专利.在我所见过的多种电池管理系统中,精度最高的两种,都是5mV,而这两种也都是用单片机完成的.采用专用的多节电池电压检测芯片,即使在软件校准条件下,也只做到20mV.
如果我没说错,5MV的精度你应用在BMS系统,而不是电动车保护板,成本和静耗是自行车所不能承受的,只有电压差分和悬浮地加上电位校正才能做到5MV的精度,但话说回来,保护板一旦精度上到25MV,工艺是一个很复杂的过程,且保护板和电池组组装往往不是同一家公司,这里面彼此必须得有很好的配合才能体现这精度的优势,否则精度越高只会出现越多的问题。比如一组电池组中,每个电池组必须通过导体连接,而这个导体根据不同在大电流情况所产生的压降也不一样,比如一个导体电阻1MR(电动车电池组连接导体通常来讲都大于3MR),电流20A,那么就有20MV的误差,也就是在物理上这导体是同一电位,而实际上,你接第一个电池的+和第二个电池的负极却是有很大的不同,所以当精度上25MV以内,就必须得引出双线,就每个电池都得对应一根正负导线,否则再高精度的系统也没有任何意义。再者更严重的就是均衡而引起的误差精度,这里就不一一详谈了。有需要交流欢迎加入电池保护系统QQ群35585132
我们目前把这种检测电路也用在了电动自行车的保护板上了,并不只限于电池管理系统中。它的电压检测电路这部分成本约为0.5元/节。功耗小于100uA(所有节数都算在一起的最大功耗)。
0。5/节我想只能做到30V以下(最多也就是40V),如果是60V以下应在0。7~0。9每节左右,顺便请教一下,如果是用在自行车上,你做这么高的精度应该是为了均衡吧,如果仅仅是检测,我想没这个必要,电池管理系统因为要做能量计算,精度所以就显得重要了。还有,自行车方案应做不了独立单片机电源供电,因为不像BMS那样可以做工作开关,既然做不了单独电源供电,那么就做不了单片机直接采样,如果不直接采样能做5MV精度真是可谓上品,我看只是个别或在一定条件测试出来而已,如果是用开关切换差分,那么运放差分本身用1%的电阻就已经超过5MV的误差,即使你用0。5%的电阻,不考虑温漂,运放失调精度和单片机采样的误差(包括模数转换的四舍五入算法),比如采集第10串40V电压,9节为36V,正常情况下,运放+相是20V,但经过0。5%的极端误差后,20。1V,那么—不考虑失调也就是20。1V,如此算来就算负相电阻不作误差算就已经4。2V,正常应是4V,再经负相电阻极端误差会更大,这是不作校正算法,作了校正后,我仔细算过,用0。5%稳压IC的作基准,也会在8mV~15MV之间,就算你用昂贵的2MV精度误差基准,如果加上以上运放失调和温漂,和算法误差,也根本做不到5mV,当然如果只测样,我不否认能测出个别正负5MV误差精度的样品来,因为本身仪表测试也有误差,但是我想你规格书并不敢大胆承诺5MV的精度,目前我只见过单片机直接采样,并且是12位精度,高精度基准源校正,才能做到5MV的承诺,如果兄台真能做到如此低价上品,不防说说一二,让大家分享分享
我的测量方法不是对高电压直接A/D的,是电压变换,直接将高端的电池电压变换成对地电压后进行检测的,因此用10bit的A/D作过采样再加软件校准后,误差就做到5mV以下了。
这个电路是我们的专利电路,现在还在保密阶段,不宜公开。
下面我贴两张图上来,一张是专利受理号的,另一张是实测结果的。
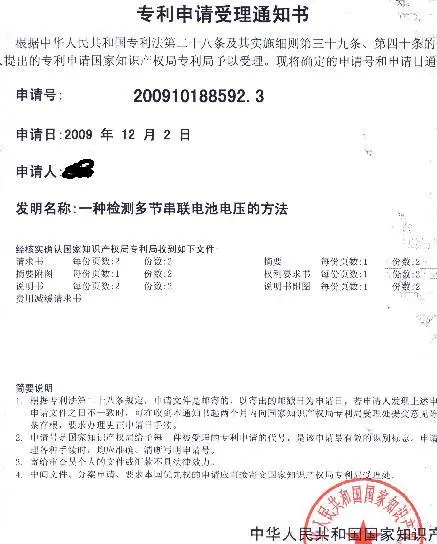
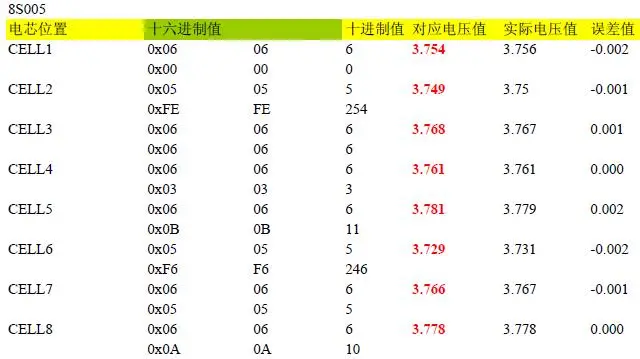
真正用于电压变换部分的,每节是0.3元。
我相信你能做出来,还是等你专利批准之后,再贴出来让大家学习一下,16串可以做到0.6左右,估计你17串成本就上去了.是不是这样的?